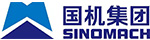
轴承套圈毛坯料大致分为以下5种:(1)锻件;(2)管材;(3)棒材(供直接切削用);(4)卷材;(5)板材、带钢。
向心球轴承及圆锥滚子轴承多使用锻件。大量使用锻件的原因是:(1)利用金属的延展性形成所要求的尺寸形状,减少了切削留量,此外,能够应用冲压机及辗压机等加工速度快的加工机床,生产率高。(2)如果去掉棒材及管材、板材的剪切加工面以及加工过程中的底部排气等,不会切断产品的金属流线,还有,材料应变使晶粒微细化,加工硬化提高了材料强度等等,能改善材料自身的性能。此外,在风力发电机组及工业机械中使用的大直径轴承,必须使用锻件。
至于小批量生产的直径较小产品,有时候在成本上不能发挥锻件的优势,这时,可应用管材及棒材。
1 向心球轴承、圆锥滚子轴承
向心球轴承内、外圈的锻造有以下方式:高温成形+冷辗;热锻+热辗;热锻+冷辗等。
1.1 高温成形+冷辗
图1 高温成形+冷辗
图1为零件高温成形+冷辗的示意图。以轴承钢棒料为原材料,经高频加热,而后在零件高温成形机内切割成规定的长度,锻造出内圈与外圈的环状坯料,然后进行球化退火、喷丸处理,最后冷辗加工。根据工件尺寸,高温成形的生产速度为100~180个/min,所需要的冷辗设备台数应与之相匹配。高温成形设备基本上是卧式多工序压力锻造机,在滑块(压力机压头)侧装有冲头;固定侧(压力机垫板)装有锻模,材料在金属模具间锻造成形。高温成形之所以高速,主要有以下原因:
(1)没有必要与重力反向来移动笨重的压力机滑块(压头);(2)工件的搬运基本上是一元的,符合压力机滑块的动作,搬运爪与金属模具并不干涉,能快速适时地移走工件,顶出杆、支承销杆的动作及金属模结构上做了精心考虑。
冷辗工序利用主辗压辊与芯轴进行辗压,扩大直径的同时,成形内、外径形状。另外,芯轴本身由于并不具备刚度,利用称为托辊(支承辊)的轧辊构件支承。并且,为提高工件的圆度,采用的主流结构形式是称为支承辊及滑靴的构件(图1中未示出)强制支承加工过程中的工件外径,并且,动作的数值控制也已实用化。
1.2 热锻+热辗
超过零件高温成形加工能力的中型轴承套圈的原材料(坯料),采用图2的工序加工。用剪切或机械加工切断棒料即成坯料,对坯料加热,用大型立式锻造压力机制造内圈与外圈的环状坯件,并利用余热,实施热辗。然后,进行球化退火、喷丸处理和外径精压加工(整形)。
图2 热锻+热辗
这种加工方式在同一温度下进行锻造与辗压加工,故热效率高,变形阻力小,工序周期缩短。但由于直接连接2道工序导致设备运转率降低,同时,为使锻造周期与辗压周期相匹配,不得不将周期时间向下设置,因而不能充分地发挥锻造工序的能力,该方式并未有效推广。
在工业机械及风力发电机组用大型轴承方面,采用了热锻+热辗加工的方法。热辗加工中,除去加工部的鳞屑对提高加工质量至关重要。此外,由于是大型轴承,削减加工余量尤为重要,尤其是像圆锥滚子轴承那样的异形截面,为尽可能减少材料损失,热锻工序的加工精度以及热辗异形断面成形加工技术至关重要。
1.3 热锻+冷辗
热锻制造环状坯料,冷却后进行球化退火和喷丸处理,进而实施冷辗。热锻的生产速度比高温成形(1.1节)低些,但通用性好,金属模具开发较为容易。冷辗工艺的工作压力比热辗工艺大。加工时间长,但是,冷辗工艺无需像热辗那样对坯料进行繁琐的温度管理。由于容易处理坯料,易实现生产自动化,产品精度也高。如图3所示,在冷辗前,进行车削加工而形成高精度的坯料,冷辗后则省略车削工序,热处理之后只进行研磨加工得到具有端面、外径面、内径面精度高的成品零件。
图3 热锻+车削加工+冷辗
1.4 热锻+冷锻
用热锻工艺制造环状坯件,进行球化退火、车削、喷丸清理之后,将磷化处理的坯料进行冷锻成形,这种情形下,能够加工的零件尺寸有限,但易提高精度。另外,如进行球化退火,则由于表面脱碳,需要有消除该脱碳层的加工。不过,已有人提出了复碳退火减少车削余量的工艺。
1.5 小结
锻造轴承套圈坯件的工厂正在向专业化、自动化方向发展,通过进一步提高金属模具寿命,金属模的小型化,提高操作性,生产效率大幅提高。随着传感器技术的进步,对加工状态和金属模具状态的监控不断进步,能够进一步降低次品率。另外,为减轻环境负担,提高产品合格率,减轻后续工序中的加工负担;生产设备的小型化、节能化;使用更环保的白色系润滑剂等,也越来越受到重视。
2 向心滚针轴承
滚针轴承常用于变速器、发动机及压缩机等,轴承安装空间狭小,需要承载能力大的应用场合。
向心滚针轴承外圈的加工成形方法有:(1)板材的冲压加工;(2)锻造坯料的切削加工;(3)管材的切削加工等。其中,板材的冲压加工占绝对多数。其原因是滚针轴承零件比球轴承零件薄,适合于冲压加工。
2.1 连续自动冲压(多工位冲压)加工
连续自动冲压加工(多工位冲压)通常是用冲剪机从卷材中冲裁圆板状的坯料,再用压力机进行深冲成形及外圈底成形、打字工序、切毛边工序等。为提高生产率,生产工序高速化是重要因素。目前,能够实现200SPM ( Slide Per Minute:冲压次数/min)。此外,基本上都是对冲压件直接进行热处理,而后只进行表面精加工。由于对冲压精度要求很高,所以对冲压设备及金属模的精度、刚度都要求非常高,因此,轴承加工用的特殊、专用机械设备也得以快速发展。另一方面,产品批量小时,与其要求和专用机械相同的生产速度,不如在减少工序数量方面精心考虑。另外,应利用廉价的通用机床削减金属模具费用,压缩生产准备时间。后一种加工方法是适合于小批量零件的加工方法。
连续自动冲压加工不必要设置实现冲压机内顺序动作加工的托架,通过在板材的供给装置上下功夫,能减少废料,提高成品率高。与顺序动作加工相比,冲压机内的送料装置(连续自动送料装置)是非常必要的,但设备费用稍高。
2.2 顺序(连续)冲压加工
连续冲压加工的优点:能够简化压力机内送料装置,容易增加工序数,适应多品种产品的冲压加工,还有容易提高加工速度。缺点为:成品率低。
可根据加工的产品形状、尺寸、批量等,选择采用连续自动冲压加工方式,或选用连续加工方式。
3 推力滚针轴承
推力滚针轴承套圈几乎都是利用冲压加工制成的。加工方法通常是采用2.2节中阐述的连续自动冲压加工方法。由于产品厚度薄,加工工序数比向心滚针轴承的外圈少,但平面度很重要,要考虑冲压加工、工序及金属模具形状。此外,推力滚针轴承的套圈难以利用冲压加工以提高与滚子接触的滚动面的表面粗糙度。因此,采用表面粗糙度好的坯料,并保持其表面状态的加工方式很重要,要在材料供给(送料)装置、成形工序、冲压机内传送、产品送出、乃至后续工序的处理等多方面予以精心考虑。
4 向心滚针轴承保持架
向心滚针轴承保持架从成形方法来看大致分为以下2类。
4.1 焊接保持架
将带钢辗成所要求的形状,利用冲压机成形为保持滚子的兜孔及卡爪之后,卷成圆管状并焊接。该方法的优点在于与其他方法相比,材料的成品率最高。
4.2 非焊接保持架
非焊接保持架的成形方法主要有以下6种。
• 管料⇒兜孔冲压⇒辗压成形;
• 管料⇒兜孔冲压⇒冲压成形;
• 管料⇒胀形成形⇒兜孔冲压;
• 管料⇒辗压成形⇒兜孔冲压;
• 管料(切削加工件)⇒兜孔冲压;
• 管料(切削加工件)⇒兜孔冲压⇒辗压成形。
圆管料(除切削加工品之外)的成形方法,有以下3种模式:切断管材;车削深冲件;深冲。各有优、缺点,可根据需要数量及成本,选择最佳工序。
4.3 小结
塑性加工的主要目标是产品的高精度和高的生产率,以及对小批量生产的适应能力。因此,冲压设备的高刚度化、高速化、小型化,以及板材的高精度是重点,小批量生产的适应能力,则需要致力于通用压力机的应用(包括省略工序),以及实现生产准备时间最短化(瞬间完成准备)等来做研究。
(来源:轴承杂志社)
轴研所公众号 轴承杂志社公众号
营销热线
0379-64367521
0379-64880626
13693806700
0379-64886322
0379-64881181