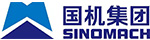
要满足轴承性能要求,以淬火硬化为目的的热处理是不可少的工序。热处理工序中所消耗的能源占轴承制造工序总能耗的25%左右。因此,从节能、环保角度,对轴承制造过程中的热处理进行分析,主要的对策包括:热处理工序的高效化;小变形热处理技术等。
1 轴承的热处理方法
以淬火硬化为目的的轴承热处理方法有多种,多数情形下可大致分为整体淬火、渗碳淬火、高频淬火、碳氮共渗等。
整体淬火是最普通的轴承热处理工艺,材料多数使用高碳铬轴承钢(GCr15)。在热处理炉中加热到840 ℃左右,并使球化退火所形成的碳化物在基体中适度、均匀地固溶,进而淬火冷却后,实施低温回火。通过未溶碳化物与回火析出的碳化物,获得均匀的析出组织,可用于要求耐磨的轴承。
渗碳淬火是在热处理炉中将低碳合金钢于930 ℃左右保温,管理炉内的渗碳性气体,从表面到内部使碳渗入扩散,进行淬火的热处理,由于碳浓度的梯度,淬火后的表面硬化,因内部比表面硬度低,用于要求耐冲击性的轴承。
高频淬火是利用感应加热的热处理,主要用于中碳钢,应用于形状复杂的汽车车轮用轴承等,只硬化必要部位。
碳氮共渗是在渗碳性气体中添加5%左右的氨,在表面层附近析出氮化物。考虑到,奥氏体中的碳与氮的溶解度差异,通常是在低于渗碳温度的750~850 ℃下进行处理,尤其是对于在混入异物的环境下使用的轴承的长寿命化最有效。
2 热处理高效化(压缩渗碳时间)
在渗碳淬火热处理中,尤其要求通过高效化以实现节能,与整体淬火的处理时间相比,渗碳淬火的处理时间长达前者的几倍到数十倍(处理时间随着轴承尺寸不同而有差异,但大尺寸轴承有时候要在炉中经过将近100 h的处理),因此消耗较多的能源,为降低能耗,缩短渗碳时间是有待解决的一大课题。
气体渗碳广泛应用于批量生产。通常,按照渗碳的机理,一般认为有2个阶段。在第1阶段是由于渗碳气体与钢材的渗碳反应,碳向钢材表面移动的阶段;第2阶段,渗碳气体与钢材表面的碳势大致相等之后,钢材表面的碳向内部扩散,表面碳势降低,由渗碳气体补充,要缩短渗碳时间有必要提高第1,2阶段的速度。
使用普通的RX气体进行气体渗碳时,为加速其第1阶段的渗碳,一般要加大渗碳气体中的CO, H2的分压力。近年来,正在着眼于改变渗碳气体中所含CO, H2的分压力,开发旨在提高渗碳速度、压缩渗碳时间的技术此外,作为替代气体渗碳的渗碳工艺,通过在称为真空渗碳的低压气氛中,使少量的碳化氢系气体直接与工件接触,以进行渗碳,提高碳在钢表面的渗入速度。
在碳扩散的第2阶段,由于碳的扩散依赖于温度,通过提高渗碳温度,可以大幅度缩短渗碳时间。不过,由于渗碳温度高,晶粒粗大化等重要原因,会导致机械性能降低,所以,渗碳温度存在不能超过晶粒粗化极限温度的问题。开发可解决上述问题的材料也是解决问题的途径。
从材料方面考虑,需开发新的材料,即容易使碳渗入钢材表面的材料。此外,通过使用高淬透性的材料,使有效硬化层深度加深,能缩短渗碳时间,但目前来看,这样的新材料价格较高。
3 小变形热处理技术
热处理过程中会发生变形,热处理后的变形量决定了后续磨削工序(图1)的磨削余量。轴承的制造工序中,仅次于热处理能耗的是磨削、组装工序,通过减小磨削余量可压缩磨削的循环时间,降低热处理变形关系到削减大量能耗。
图1 轴承的普通制造工序
以轴承钢热处理时的尺寸变化(图2)为例,随着加热时的温升,发生热膨胀与奥氏体化,并在冷却时产生热收缩,马氏体相变时产生热处理变形。这样一来,热处理时有很多引起尺寸变化的要素,由于该尺寸变化时产生偏差,而发生热处理变形。该尺寸变化的偏差,是加热、冷却时的温度偏差引起,均匀地加热、冷却可降低热处理变形。
为此,防止热处理变形的对策有以下几种:以降低加热时的温度不均为目的的多级升温;以降低冷却时的温度不均为目的的多级冷却;还有淬火油种类、油槽搅拌速度的最优化之类的措施。近年来,也在采取其他对策:如,通过模拟热处理时油槽内的油液流动,进行分析,开发形成均匀油液流动的油槽;通过改善热处理夹具,能实现均匀加热、冷却。
此外,尤其在容易发生热处理变形的薄壁轴承方面,根据热处理时温度与尺寸变化的关系(图2)进行淬火(压模淬火)。如果是轴承钢,经整体淬火引起的相变导致尺寸膨胀,在Ms点之后,约束外径侧,并用压力机一边控制工件上下方向,一边完成淬火。由于渗碳淬火完成后尺寸几乎没有改变,淬火过程中发生热收缩,一边用压力机控制并约束内径侧,一边实施淬火,进而大幅度地降低热处理变形(图3)。
在热处理的尺寸变化时,利用该变化进行约束淬火是降低热处理变形的有效对策之一。轴承并不像齿轮那样形状复杂,由于形状简单,一直在实施约束淬火,不过,约束淬火的热处理成本比普通热处理费用高是有待解决的问题。
图2 热处理时温度与尺寸变化
图3 约束淬火方法
因此,开发出不产生热处理变形的热处理技术,是一项有意义的研究工作。针对影响钢材变形的因素,也可采取适当的对策,例如,减少材料偏析,在不进行锻造工序时,降低材料的残余应力等。
小结
上面阐述了轴承的几种典型热处理方法,与以节能为目的的高效化与低变形热处理技术,但为了适应减轻环境负担的要求,热处理工序方面发挥更大的作用,进一步提高技术水平是不可缺少的,有必要以节能为核心,进一步实现低成本化。
(来源:轴承杂志社)
轴研所公众号 轴承杂志社公众号
营销热线
0379-64367521
0379-64880626
13693806700
0379-64886322
0379-64881181