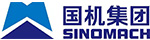
导读
剖分三排圆柱滚子转盘轴承分段多,尺寸大,质量大,加工时装配精度低,整圈淬火变形大,接缝处应力大,径向及圆周方向间隙不易调整,配制游隙时修磨滚道次数多,传统高速钢材料刀刃易磨损。提出改进措施:加工和拼接时增加专用胎具;采用分段、分面淬火,淬火后增加整形工序;设计径向定位夹具调整径向间隙,设计切向定位夹具调整圆周方向间隙;通过轴向游隙推算所需加工的内、外圈轴向滚道尺寸;软车采用带涂层的硬质合金刀具,硬车采用立方氮化硼(CBN)刀具完成以车代磨等。最终确定的工艺路线满足了轴承加工所需的技术要求。
随着海工装备技术日趋成熟,海工行业大型起重机已经向超大尺寸、超大吨位发展,与其配套的转盘轴承直径达10 m以上。该直径段的转盘轴承结构多为剖分式,其优点是便于运输、储存及拆装,缺点为需要多次拆分、拼接,加工工艺复杂,加工精度难以保证,故需确定合适的加工工艺。
1、超大型剖分三排圆柱滚子转盘轴承结构
某剖分三排圆柱滚子转盘轴承结构如图1所示,采用阶梯搭接,轴向用铰制螺栓定位连接(图2)的方式组合成整体内、外圈,装配后轴承内圈沿内径方向展开如图3所示。
该剖分轴承最大外径为12.3776 m。高度为0.6 m,最大壁厚为489 mm,内外圈共分为18段。技术要求:装配高为(600士2) mm,轴向游隙为1.2 ~1.8 mm,径向游隙为0.5 ~1.2 mm,轴向跳动不大于0.6 mm,径向跳动不大于2 mm。
1)轴承直径超出机床工作台加工范围。
2)在推力滚道上剖分切口会与滚子素线形成一定夹角,使滚子能通过切口。为保证齿轮强度受影响小,将外齿圈剖分切口切在齿槽底中心位置,增大了铣连接面及拼接整圆的难度。
3)剖分轴承直径大,加工过程中剖分段因自重下坠倾斜,两端面及轴向滚道平面度、倾斜度大,径向滚道圆度、圆柱度超出工艺要求,装配后轴承旋转精度不能满足要求。
4)外齿圈淬火面总长度为490 mm,属大截面滚道淬火。整圈淬火时剖分段会出现不规则变形(图4),变形后无法拼接成整圆,影响后序加工。整圈淬火后接缝处应力较大,套圈会从接缝处脱开。整圈尺寸大,淬火机床回转困难。
3、方案制定
3.1 工装夹具
剖分轴承在胎具上加工,为便于吊装,胎具也采用剖分结构。整个胎具分为4段,连接方式为上下搭接,轴向用锥销定位,加双排螺钉紧固(图5)。
胎具材料选用具有较高屈服强度和抗拉强度的ZG380-510铸钢,保证胎具刚度胎具为剖分轴承加工提供了可靠的刚性支承,可减小各工序加工变形,保证加工精度。
为拓展机床加工范围,重新制作专用方箱、支座以及配套的T形块、螺杆、挡板、压板、垫块等,解决了大直径轴承超范围加工问题。
3.2 装夹方式
加工时要考虑胎具与剖分轴承的装夹方式,以内圈主推力滚道加工为例,内圈装夹如图6所示。方箱底部设计2排连接孔,通过螺栓与机床工作台连接。卡爪将胎具卡紧并用压板固定。内圈放置在胎具上,长挡板顶紧外径面,压板压紧内圈端面。胎具和内圈进行轴向和径向定位,固定点数量是轴承分段数的3倍,防止零件加工中出现平移。
3.3 拼接整圆
剖分面为台阶形状,要求拼接轴向间隙不大于0.1 mm,径向间隙不大于0.3 mm。拼接会影响轴承加工精度,因此要保证外齿圈剖分切口在齿槽底中心位置。工艺上选择先划出成品齿形及精铣连接面剖分线(图7),其轴向和圆周贴合面均在数控龙门铣床上加工。通过程序设定、预先模拟调整每段弧长及2个结合面的角度和尺寸,多次研配结合面以确保连接精度,待连接整圆后依次配对编号。
剖分轴承在加工中需多次吊装、拼接、拆分,为保证成品连接精度,在前工序加工时采用小尺寸的工艺锥锥孔。通过锥销对每段连接点定位后连接加工。终加工时将定位锥销孔加工成铰制螺栓孔,保证零件连接可靠。
3.4 淬火方案
选取分段、分面淬火。为方便吊装,淬火前加工吊装孔。为减小淬火变形,在套圈上设置端面台阶,胎具设置凹槽(配合间隙1~2 mm)进行限位。另外,在胎具上加工与套圈吊装孔位置一致的螺纹孔,用螺钉将套圈与胎具固定(图8)。
3.5 整形方案
淬火后每段曲率不规则,不成正圆,总趋势为外圈弦长减小,内圈弦长增大。套圈壁厚较大,淬火后需进行热整形。整形要求如下:
1)对比淬火前、后每段弦长变化,确定整形量,选定整形位置;
2)火焰温度为700~800℃,加热时控制加热面积,防止产生新的变形,加热后浇注冷却液;
3)粗整形,以实际弦长为依据(不需要在机床上进行);
4)精整形,边整形边测量每段圆周跳动(在机床上进行) ,使每段均符合工艺要求;
5)整形后测量每段尺寸是否达到整形要求。
3.6 装配方案
剖分轴承精加工、装配均以淬火、 整形后每段连接面处轴向、径向间隙做为拼接基准。装配方案:先吊取第2内圈,按编号依次完成拼接,通过径向定位夹具调整径向间隙(图9),通过周向定位夹具(图10)调整圆周方向间隙,然后用校对样板内圈半径R2(图11)校验接缝处曲率,通过铰制螺栓连接,完成第2内圈装配。再按照常规三排圆柱滚子转盘轴承的装配方法组装成整套轴承。内、外圈装配方法参考第2内圈。
调整径向间隙时,将夹具放置在套圈端面上,螺杆顶紧轴承内、外径面,通过螺杆调节。调整圆周方向间隙时,将螺纹孔定位销与光孔定位销分别放在连接缝处的2个安装孔内,通过螺杆紧固调节。
3.7 轴承游隙
通过轴向游隙推算所需加工的内、外圈轴向滚道尺寸,可减少滚道修磨次数,从而减少吊装、拼接次数,提高加工效率。轴向游隙计算示意图如图12所示,轴向游隙Ga=b+c-a-d-d2。
剖分轴承分段拼接,每段外齿圈会因自重下坠倾斜,普通三点测量轴向游隙已不适用。轴向游隙测量如图13所示,虚线、实线分别为轴承组装后的实际位置和理论位置。千斤顶与百分表位置均会对轴向游隙产生影响,测得A点值比B点大,B点值更接近实际游隙。采用单点测量轴向游隙,千斤顶与百分表位置靠近轴承内圈,在每段中间部位及连接缝处各取1个点,共计12个点或更多,取其平均值作为实测轴向游隙。
径向游隙的配制:试配初始径向游隙→确定滚子尺寸→修磨滚子。
径向游隙的测量:第2内圈、轴向滚子与外圈装配后,在连接缝处及每段中间部位(共计12处),装入径向滚子(为保证径向游隙测量准确,采取无间隔并排滚子,要求每组滚子数量不少于30粒),测量径向滚子与内、外圈间隙,取其平均值作为实测径向游隙。
3.8 选择刀具及加工参数
精加工余量小,可使用带涂层的硬质合金刀具完成车削,该刀具硬度达69~81 HRC,车削平稳,耐磨性好,切削速度是普通高速钢的4~7倍,提高了加工效率。硬质合金刀具加工参数为:机床转速2 r/min, 进给量0.4~0.7 mm/r。
滚道表面淬火后硬度为57~62 HRC,终磨滚道前先硬车去除滚道淬火变形较大部位,可减小后续磨加工留量,大幅提高加工效率。硬车使用立方氮化硼(CBN)刀具完成以车代磨。CBN是超硬刀具材料,硬度高和耐磨性好,用于对淬硬钢(硬度45~65 HRC)的精加工,也可用于精车断续表面,但在断续加工中,不能使用冷却液。CBN刀具加工参数为:机床转速2.5 r/min, 进给量0.08~0.2 mm/r。
4、确定工艺流程
4.1 初步工艺流程
根据剖分轴承的结构特点,初步确定工艺流程:锻件→粗车→铣连接面→拼接整圆→钻、铰工艺锥销孔→半精车→滚道表面淬、回火→整形→精车→钻孔→硬车滚道→终磨→配游隙→装配。
该流程存在以下问题:
1)粗车切除材料较多,应力不能完全释放;
2)淬火后变形量(端面翘曲、径向跳动)大,影响后序加工;
3)热整形温度高,整形部位有较大内应力,易出现裂纹。
4.2 优化工艺流程
对上述问题分析,认为剖分轴承加工重点是要控制热处理变形,保证整形质量,最终确定优化后的工艺流程为:锻件→粗车→去应力退火→半粗车→粗铣连接面→振动时效→精铣连接面→拼接整圆→钻、铰工艺锥销孔→半精车→钻、攻吊装孔→附加回火(温度170 ℃±10 ℃,炉内保温4 h±0.5 h)→滚道表面淬、回火(温度170 ℃±10 ℃,炉内保温8 h±0.5 h)→整形→附加回火→精车→钻孔→硬车滚道→终磨→配游隙→装配。
优化后的工艺流程具有以下优点:
1 )淬火前增加附加回火,可及时消除或减小前工序产生的残余应力,进而减小淬火变形;
2)热整形后增加附加回火,可防止整形开裂。
5、实际加工效果
采用优化工艺加工后轴承的各项技术指标检测结果见表1,满足技术要求。轴承交付使用后,未发现异常现象。
(来源:《轴承》2021年6期)
轴研所公众号 轴承杂志社公众号
营销热线
0379-64367521
0379-64880626
13693806700
0379-64886322
0379-64881181