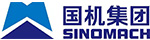
变桨轴承是风力发电机组的关键部件,使用环境恶劣,维修成本高,受力情况比较复杂,并且直接影响整个变桨动作的连贯性、稳定性以及准确度,为保证变桨轴承寿命的可靠性,需要对变桨轴承进行良好的密封及润滑。随着风电机组运行时间的增加,变桨轴承的密封圈逐渐老化,润滑脂逐渐变质,废脂外排不畅和变桨轴承不完全回转造成内部压力不均等均会导致变桨轴承密封圈处出现不同程度的漏脂,若不及时处理可能会造成变桨轴承润滑不良,从而影响变桨轴承及风电机组的使用寿命。变桨轴承漏脂的原因较多,由于跟踪观察及验证周期长,密封试验台难以模拟变桨轴承实际工况等原因,对其研究不够系统、深入,因此有必要对变桨轴承漏脂的原因进行分析和总结。
变桨轴承漏脂的原因
1 密封不良
1.1 密封圈老化与磨损
变桨轴承大多采用丁晴橡胶密封圈,长时间使用会发生老化,其老化速度与丁腈橡胶中丙烯腈含量、配方含胶率、防老剂以及使用环境等因素有关,一般情况下丁晴橡胶密封圈使用寿命为5~10年。变桨轴承采用接触式密封,在运行过程中密封圈与密封摩擦面接触,随着运行时间的增加,密封圈会逐渐磨损导致密封性能下降和密封圈承压不足,润滑脂可能会从密封圈处泄漏。
1.2 密封圈结构设计不合理
变桨轴承一般采用双唇密封圈,其外唇可阻挡水分、灰尘及其他有害物质侵入轴承内部,内唇可防止漏脂。若密封圈结构设计不合理,安装后会影响密封效果,并且变桨轴承运行后可能会导致密封圈变形,使密封能力不足或密封失效,润滑脂容易泄漏。
1.3 密封圈安装与维护不当
不按照工艺安装或维护时会导致密封圈受力不均匀,安装密封圈时接口粘接不良会导致密封圈接口断裂,后续变桨轴承注脂运行后密封圈容易出现鼓包、翘曲(图1)和断裂现象,从而使润滑脂从密封圈缝隙、翘曲及破损处溢出。
图1 变桨轴承密封圈翘曲
1.4 密封圈挤压损坏
风电机组的叶片安装或维护时需要使用液压拉伸器对叶片与变桨轴承的连接螺栓施加力矩,连接螺栓与密封圈的距离较近,且液压拉伸器的拉伸头外形尺寸较大,拉伸头易压到密封圈使密封圈严重破损,如图2所示。变桨轴承后续运行时可能会导致密封圈变形和撕裂,造成润滑脂大量泄漏。
图2 变桨轴承密封圈挤压破损
2 变桨轴承内部结构设计不合理
2.1 沟道结构
变桨轴承沟道设计影响润滑脂在轴承内部沟槽的流动性。正常情况下,变桨轴承从注脂孔加注润滑脂,从排脂孔排废脂需要的压力差值小于密封圈所能承受的压力值,同时大于润滑脂流动的阻力值,则密封圈处不会漏脂。所需的压力差值与润滑脂流动的阻力密切相关,阻力小需要的压力差值就小,阻力大需要的压力差就大。若变桨轴承内部沟道设计不合理,润滑脂流动阻力就大,不利于润滑脂与内部压力的均匀分布,润滑脂无法顺利进入排脂孔而造成排脂不畅,导致密封圈处润滑脂溢出。
2.2 脂孔尺寸与分布
变桨轴承的注脂孔和排脂孔需合理间隔分布,保证轴承能顺利注入新脂并排出废脂。相邻注脂孔与排脂孔的距离要适中,若距离太短,加脂时注脂孔压力较大而排脂孔压力较小,新加的润滑脂易从排脂孔排出;若距离太长,加脂时密封圈承受的局部压力较大,易导致漏脂。另外排脂孔截面直径过小,与排脂孔相连接的集脂瓶口直径过小,轴承上相邻两排脂孔的间距过大,也会增加润滑脂排出的阻力,造成排脂不畅,使变桨轴承内部压力过大导致漏脂。
3 润滑脂选择不当或润滑系统设置不合理
3.1 润滑脂选择不当
润滑脂的选择通常要参考变桨轴承的实际工况,同时还需考虑润滑脂的稠度和添加剂种类等。润滑脂的稠度与周围环境温度密切相关,环境温度每下降5 ℃,稠度会增加1倍,润滑脂流动性将会变差,如果润滑脂的稠度不合适或抗压性能不足,后续使用易发生固化现象而堵塞脂路系统,导致润滑脂无法正常排出而从密封圈处泄漏,如图3所示。
图3 变桨轴承排脂孔处的固化润滑脂
3.2 注脂量及集中润滑系统设置不合理
变桨轴承在运行前需填充一定量的润滑脂,填充量约为变桨轴承内部空间的60%~80%,一般选择的填充量约为70%,也有个别变桨轴承供应商为了保证充分润滑选择80%的填充量。
国内外风电机组大多采用集中润滑系统对变桨轴承加注润滑脂,部分风电机组制造商为进一步降低变桨轴承的维护成本采用人工定期加注润滑脂。这2种加注润滑脂的方式均存在不足:人工定期加注润滑脂的注脂量及注脂周期往往为经验数据,与变桨轴承实际所需润滑脂存在较大偏差,注脂量通常情况下会偏多且不均匀,无法保证变桨轴承的润滑时间,再加上变桨轴承出厂前可能加注了约80%的润滑脂,极易造成变桨轴承沟道内局部润滑脂大量堆积;集中润滑系统采用自动注脂方式,使轴承润滑更加充分,虽然保证了变桨轴承的润滑时间和注脂量的均匀性,但在变桨轴承不运行或机组长时间停机状态下,集中润滑系统仍按其预设好的固定程序继续注脂,同样容易造成变桨轴承沟道内局部润滑脂大量堆积。
正常情况下变桨轴承密封圈的密封压力约为2.8x105 Pa,变桨轴承静止不工作时所需注脂压力约为(2.5~2.8) x105 Pa,变桨轴承运行时所需注脂压力仅为0.6 x105 Pa左右。因变桨轴承所采用的润滑脂本身流动性较差,上述2种注脂方式导致的润滑脂大量堆积会增大变桨轴承沟道内润滑脂通道的压力,从而增加注脂时所需的注脂压力。当注脂压力大于变桨轴承密封圈的密封压力时,润滑脂会在注脂推力的作用下从变桨轴承密封圈处大量泄漏。
另外,如果集中润滑系统的压力泵或输脂管中的空气未完全排空,空气将随着润滑脂进人变桨轴承沟道,造成沟道内局部压力过大,当该压力大于变桨轴承密封圈的密封压力时会撑开密封圈,造成严重漏脂现象。
3.3 废脂收集方法不当
目前风电机组变桨轴承废脂收集普遍采用在轴承圆周上分布的数个废脂排出小孔分别安装集脂瓶的方式,加入新脂时,新脂把废脂从轴承内腔挤压进废脂排出小孔,排入集脂瓶,需定期清理。实际上,随着变桨轴承运行时间的增加,废脂收集效果不好,容易漏脂。
未完待续
(来源:轴承杂志社)
轴研所公众号 轴承杂志社公众号
营销热线
0379-64367521
0379-64880626
13693806700
0379-64886322
0379-64881181