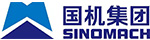
解决措施
1 密封圈
1.1 选择质量可靠的密封圈材料
国内密封圈的抗老化、抗磨损等关键性能与国外还有一定差距,当前大多风电机组制造商采用成本较高的进口密封圈材料。
1.2 改善密封圈的结构
目前国内大部分变桨轴承密封圈采用类似双唇的结构,如图4所示,结构简单,防止内部漏脂的能力有限,因此在原有结构基础上进行优化,将双唇结构改为多唇结构(图5) ,同时增加2道直密封唇加强防泄漏效果,其安装示意图如图6所示。
图4 变桨轴承原密封结构
1—凸台;2—主密封体;3—防尘唇;4—第3道封油唇;5一第2道封油唇;6—第1道封油唇;7—第1道直密封唇;8—第4道封油唇;9—第2道直密封唇
图5 新型防泄漏密封圈截面示意图
图6 新型防泄漏密封安装示意图
第1道封油唇前端与变桨轴承内圈的外圆表面紧密接触,末端与外圈的内圆表面紧密接触,其外侧凸起的弧面有利于抵消变桨轴承内部的润滑脂压力,可防止润滑脂从第1道封油唇与内外圈之间的间隙泄漏。
第2道、第3道封油唇外形呈鱼尾状,其与内圈外圆表面上的密封槽接触,两者之间存在微小的间隙,丁晴橡胶密封圈具有一定的弹性,既能保证变桨轴承正常回转,又能防止从第1道封油唇泄漏的润滑脂继续向外泄漏。
第4道封油唇与外圈的嵌槽接触,可防止变桨轴承泄漏的润滑脂继续向外泄漏。
防尘唇外形呈鱼鳍状,末端与内圈的外圆表面紧密抵靠,其外侧面凸起的弧面不仅保证了防尘唇与内圈紧密抵靠,而且利于加工。防尘唇具有双向防护的特点,既能防止泄漏的润滑脂继续向外部泄漏,又能防止空气中的灰尘、杂质或其他有害物质进入到变桨轴承内部导致沟道磨损或发热卡死,造成风电机组无法正常工作,甚至出现重大事故。
第1道、第2道直密封唇与外圈表面接触,可防止泄漏的润滑脂继续向外泄漏。
凸台位于主密封体上,上表面为平面,同时与防尘唇之间预留了安装工具操作空间,可使用带滚轮结构的操作工具沿凸台上表面前后滚压,将密封圈压实,从而保证密封圈的密封效果。
新型防泄漏密封圈整体外形呈鱼骨形,采用1道防尘唇、4道封油唇、2道直密封唇,可有效杜绝轴承内部润滑脂向外泄漏。
1.3 合理维护并及时更换损坏或老化的密封圈
必须严格按规定的工艺安装或维护密封圈,避免密封圈安装不合格或密封圈损坏的情况。对漏脂变桨轴承密封圈进行检查,如发现密封圈存在老化、磨损严重、破损、翘曲变形等情况,需及时清理漏脂,并按工艺要求更换新密封圈。
1.4 缩小液压拉伸器拉伸头尺寸
与液压拉伸器供应商进行技术沟通,缩小拉伸头外形尺寸,避免液压拉伸器现场作业时挤压损坏密封圈;进一步规范现场安装工艺,增加一项“液压拉伸器现场作业时,检测拉伸头与密封圈距离”的工序。
2 改善变桨轴承内部结构
2.1 沟道底部沟槽
变桨轴承沟道结构设计不仅影响润滑脂在轴承内部沟道的流动性,也影响与沟道相连接的一段排脂孔的直径。润滑脂的流动性与其流经的截面形状及面积有关,截面越小,流动性越差。
某供应商设计的变桨轴承沟道内部结构如图7a所示,沟底全部为圆弧过渡,经风场实际验证这种沟道截面形状不利于润滑脂在沟底的流动。改进后的沟道截面形状如图7b所示,沟底增加了矩形沟槽,从而增加了润滑脂的流动性。试验结果表明,沟道截面形状改进后润滑脂可从排脂孔顺畅排出,且密封圈无鼓包、漏脂现象。
图7 某变桨轴承沟道结构
2.2 改善轴承脂孔尺寸与分布结构
GB/T 29717—2013《滚动轴承风力 发电机组偏航、变桨轴承》规定变桨轴承注脂螺纹孔规格一般为M10 mm×1 mm,排脂螺纹孔规格为M14 mm×1.5 mm,当有特殊要求时排脂孔数量、位置和规格由轴承制造商与风电机组制造商协商确定。注脂孔与排脂孔结构如图8所示。
图8 注脂孔和排脂孔结构示意图
由图8可知,整个排脂通道为阶梯结构,分为轴承外侧与集脂瓶相接的螺纹孔部分和靠近轴承内侧与沟道相连接的光孔部分。润滑脂流经的截面面积越小,排出时阻力越大,因此,在轴承结构允许的情况下,适量增加轴承排脂孔外侧连接螺纹孔的直径和深度,尽量使排脂螺纹孔接近沟道,以减小润滑脂排出的阻力。排脂孔靠近沟道的光孔部分由于受沟底设计槽宽限制,一 般直径为9 ~12 mm,若改善轴承沟底结构,增大槽宽,可考虑增加排脂孔靠近沟道的光孔部分的直径,有利于排脂。
变桨轴承排脂孔与注脂孔一般均为间隔分布,排脂孔轴向位置处于沟道中心。
3 合理选择润滑脂及集中润滑系统设置
3.1 选择合适的润滑脂
根据变桨轴承的实际工况、润滑脂的稠度及其与密封圈的兼容性等选择合适的润滑脂。润滑脂使用温度为-40~150℃,应具备抗微动磨损性、极压性、抗水性、防腐性和泵送性良好等性能。
3.2 选择合适的注脂量及润滑系统控制策略
强制要求变桨轴承最多只能加注70%的填充量,且使用集中润滑系统,不建议采用人工注脂的方式。
考虑到变桨轴承不运行或机组长时间停机状态时集中润滑系统仍按其预设好的固定程序继续注脂,因此需对集中润滑系统的控制策略进行优化,更改注脂控制方式为变桨轴承运行时注脂(此时所需注脂压力远小于密封圈的密封压力),不运行时不注脂。同时参考变桨轴承变桨的角度、速度、时间及累计变桨时间等因素设计控制策略,确定注脂的频率、时间等各项指标。另外,集中润滑系统应根据现场的外界温度进行调整,低温时润滑脂的稠度大,泵送性较差,此时需要提高注脂频率;高温时润滑脂的稠度小,泵送性较好,此时需要降低注脂频率。
针对集中润滑系统的压力泵或输脂管中的空气未完全排空造成漏脂的问题,可以在集中润滑系统安装完成后,与变桨系统进行联合调试,通过实际运行集中润滑系统检验变桨轴承沟道中是否有残存空气并进行充分排除。
3.3 增加废脂清除系统
如图9所示,废脂清除系统的工作原理为:启动液压泵,压力油通过动力管A驱动废油吸排脂器将轴承内的废油吸入吸排脂器内腔,然后分控箱启动二位四通阀,系统换向,压力油通过动力管B驱动废油吸排脂器将排脂内腔中收集到的废脂通过集废油管集中收集到集油箱。
另外可采用真空袋代替集脂瓶来收集废脂,或者缩短废脂排出管路,增大集脂瓶管口直径等方法来改善废脂不易排出的情况。
1一动力管B;2—集油箱;3—液压泵;4—废油吸排脂器;5—分控箱;6—动力管A;7—集废油管
图9 废润滑脂清除系统结构原理图
(第一部分请见网站;风电机组变桨轴承漏脂分析及改进措施(1))
(来源:轴承杂志社)
轴研所公众号 轴承杂志社公众号
营销热线
0379-64367521
0379-64880626
13693806700
0379-64886322
0379-64881181