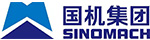
阐述利用钎焊、激光熔覆、电弧喷涂、电弧堆焊等增材技术替代常规离心铸造制造滑动轴承的优势及目前的技术水平,以及随增材制造技术而研发的高温抗蠕变巴氏合金线材成分,线径1.6 mm的细线材加工技术现状,展望了增材制造应用在滑动轴承领域以及巴氏合金线材成分优化和相关配套技术的发展趋势,对过细SnSb相是否会加速轴径的磨损和多次电弧堆焊增材是否会影响结合强度的问题进行了探讨。
以锡基巴氏合金为减摩层的滑动轴承适用于低速、重载工况,具有精度高,抗振性好,工作平稳可靠,噪声小和寿命长等优势。传统技术手段是在碳钢的钢背上采用离心浇铸或重力浇铸制取钢背-巴氏合金双金属轴瓦。铸造工艺虽然技术成熟,但存在以下不足:结合强度偏低且不稳定,铸造层较厚(一般为13 mm以上),组织粗大和偏析,裂纹缩孔等;工艺流程长,需经巴氏合金熔化、钢背挂锡、熔体注入铸造腔体、离心浇铸成型、冷却水喷淋、机床粗加工和精加工等,能耗和材料消耗大;环境安全职业健康(EnvironmentSafety Health, ESH)不够理想,浇铸过程受人为因素影响较多,导致质量一致性不高;在使用寿命、可靠性方面与国外存在明显差距。采用增材制造技术符合轴瓦发展的必然趋势,可解决铸造存在的诸多不足,尤其是能够缩短工艺流程,增材层厚度只有铸造层的25%~30%,节约70%~75%的巴氏合金材料,人为因素减少,ESH更友好,可以推动行业技术的升级换代。
近年来滑动轴承的制造发展较快,钎焊、喷涂、堆焊、增材等工艺不断迭代,大大推动了我国滑动轴承材料乃至零件制造水平的发展。增材制造是以三维模型数据为基础,通过材料堆积的方式制造零件或实物的工艺。喷涂和堆焊都可进行增材制造,但需围绕增加材料的厚度形状、性能、效率和精度进行合理选择。若增加涂层厚度只有微米级,一般看作表面处理,喷涂更多应用于表面处理,若厚度达到毫米级甚至更大,增加的材料更多,就更符合增材制造。另外,增材制造使形状复杂零件的加工流程缩短,比如多个合金面用一台设备、一道工序连续完成。激光作为加热源在表面处理方面应用较多,也可用于增材制造。
下面详细阐述目前国内电弧增材制造技术应用于轴瓦领域的现状,有关配套锡基巴氏合金的成分研究及其线材制造技术水平,探讨增材制造在轴瓦领域的应用,锡基巴氏合金线材和相关配套技术的发展趋势及存在的问题。
国内外轴瓦增材制造技术的发展
1.1 国外
21世纪初,美国摩根精密轴承公司在上海投资成立摩根油膜轴承(上海)有限公司,并在国内率先采用氧-乙炔自动钎焊设备,在轴瓦钢背上增加一层锡基巴氏合金。主要设备、钎焊线材和辅助材料均从美国进口,主要为轧钢机械配套。虽然该技术比铸造技术先进,但钎焊前要有严格的清理工序且需在钢背上涂专用助焊剂,增加了生产成本,适合大中型滑动轴承,因此应用范围受到限制。
三菱和大同等公司早期也开发了喷涂工艺和电弧堆焊工艺,但应用场合有限。由于国外公司技术保密,至今仍不清楚国外目前技术的应用情况,但从巴氏合金原料判断,其应用技术主要是喷涂和钨极惰性气体保护( Tungsten Inertia Gas , TIG)电弧堆焊技术。德国RENK公司在应用巴氏合金丝材进行轴瓦修复的技术上也在开发新的增材制造技术。
1.2 国内
1.2.1 早期的修补应用
锡基巴氏合金熔点低,易于钎焊,氧-乙炔钎焊最先用于大中型滑动轴承的修复,如离心铸造轴瓦加工后的缺陷或锡基巴氏合金层局部磨损、脱落,钎焊采用手工操作,仅限于修补滑动轴承,无法替代铸造技术并实现规模化生产。文献[8]给出了巴氏合金钎焊层的质量评价规范,详述了焊接的一般要求、焊接线材、辅助材料(纯锡或锡银合金为过渡层、助焊剂)、焊前准备、焊接过程(基体预热、过渡合金层焊接、巴氏合金工作层堆焊)、检查和验收,是对钎焊修复轴瓦过程进行规范和结果评判的依据。
1.2.2 钎焊涂敷锡基巴氏合金层
文献[9]对锡基巴氏合金( SnSb11Cu6)/钢基体过渡层组织进行研究,结果表明锡基巴氏合金/钢过渡层的显微硬度随钎焊温度的升高而明显提高,该研究未给出结合强度的试验数据。研究结果肯定了钎焊技术获得的轴瓦性能优于铸造。
1.2.3 激光熔覆技术
文献[10]采用激光重熔技术提高轴瓦性能,在轴瓦的锡基巴氏合金离心浇铸层表面采用激光进行扫描重熔,然后对重熔前后试样进行对比,结果表明激光重熔可消除离心浇铸锡基巴氏合金的化合物粗大、偏析和气孔等缺陷;重熔层的组织质量和性能大幅提高,但该研究未给出结合强度的变化对比。文献[11]研究了激光在钢背上熔覆锡基巴氏合金粉末(SnSb11Cu6)获得锡基巴氏合金层,其方式是在低碳钢表面利用高能激光束熔化金属表面形成熔池,并将合金粉末同步输送入熔池最终形成熔覆层,研究表明其熔覆层形貌良好,实现了冶金结合,中间界面层厚度约6 μm,厚度分别为2,3 mm的锡基巴氏合金层结合强度可达到45.185,59.020 MPa。
1.2.4 热喷涂技术
文献[12]采用氧-乙炔火焰喷涂制造锡基巴氏合金轴瓦,试验采用锡基巴氏合金(SnSb8Cu4)线材,除常规表面清理外,还需预先在钢背上火焰喷涂100 μm厚的Ni-Al复合丝作为过渡层,结果表明轴瓦的使用寿命较为理想,但试验未给出喷涂层的孔隙率、结合强度等参数。文献[13]研究电弧喷涂锡基巴氏合金(SnSb8Cu4)层在润滑条件下的磨损性能,对比了电弧喷涂、铸造以及电弧堆焊方法制备的锡基巴氏合金层与钢背的磨损表现,给出了在润滑条件下电弧喷涂锡基巴氏合金涂层具有比铸造锡基巴氏合金层更好的减摩性能的结果,该研究认为电弧喷涂获得的锡基巴氏合金增材层组织结构优于铸造和堆焊层;电弧喷涂层的固有孔隙特性可起到储油、润滑作用,但未进一步研究喷涂层的孔隙率和结合强度。
文献[14]研究电弧喷涂技术制造锡基巴氏合金(SnSb11Cu6)轴瓦增材层,表明虽然增材层抗磨性较好,但结合强度测试数据最高不超过17.5 MPa,其正面孔隙率为1.74%。文献[15]研究结果表明,电弧喷涂的锡基巴氏合金层经170~300°C融合4h后,结合强度可提高到50 MPa左右。
根据某滑动轴承制造企业引进电弧喷涂技术的数据,数次喷涂才能达到所需的增材层厚度,材料利用率只有30%左右,喷涂期间基体温度需保持在200°C左右。
1.2.5 电弧熔覆技术
电弧广泛应用于金属焊接,作为增材制造的热源应用于锡基巴氏合金轴瓦制造领域是近10年来才发展起来的一项新技术。文献[17]以SnSb11Cu6为研究对象,研究了熔化极惰性气体保护( Metal Inertia Gas,MIG)堆焊工艺对锡基巴氏合金轴瓦组织及性能的影响,结果表明:增材层组织方面,离心铸造的轴瓦锡基巴氏合金层组织粗大,SnSb硬质相尺寸达到95 μm左右,同时存在严重的组织偏析现象,而MIG堆焊工艺的组织细小、均匀,SnSb硬质相尺寸不超过17 μm,同时未观察到明显组织偏析;结合强度方面,铁元素向锡基巴氏合金层内扩散距离约为5μm,离心铸造仅约0.5 μm,离心铸造轴瓦断口主要特征为粗大的SnSb相颗粒发生的穿晶解理断裂,MIG堆焊工艺断口的主要特征为撕裂棱、树枝状Sn5Cu6及二次裂纹,测试数据表明MIG堆焊工艺结合力比离心铸造提高1倍,达到80 MPa左右,该研究未述及所测试样的锡基巴氏合金层厚度。以SnSb11Cu6,SnSb8Cu8和SnSb8Cu4为研究对象,进一步研究MIG堆焊工艺的锡基巴氏合金轴瓦结合强度,得出SnSb11Cu6 , SnSb8Cu8和SnSb8Cu4的结合强度分别为66.42,75.72,83.07 MPa,并给出Sb含量是影响结合强度的主要原因,该研究未给出所测试样的锡基巴氏合金层厚度。
MIG焊和TIG焊技术在增材制造领域的优势为国内轴瓦制造领域技术更新换代奠定了基础。2010年以来,国内数家高等院校联合轴瓦和锡基巴氏合金线材生产企业开始研究MIG焊和TIG焊作为增材制造技术在轴瓦领域的应用:哈尔滨工业大学与太原重工油膜轴承分公司联合建立了MIG焊工艺数据库,在国内首先完全替代了离心铸造工艺;东南大学与申科滑动轴承股份有限公司合作,引进多条基于MIG焊的增材制造生产线,逐步在大中型尺寸轴瓦和全部平面轴瓦加工中替代铸造技术;哈尔滨电机厂机电工业有限公司也引进了MIG焊技术逐步替代离心铸造技术;首先进人中国的摩根油膜轴承(上海)有限公司也开始引进MIG焊或TIG焊技术替代钎焊工艺。
MIG堆焊过程中锡基巴氏合金线材作为自耗电极不断熔化,且其线径不超过1.60 mm,熔化形成的熔滴易在大电流的作用下产生爆断飞溅,输入的电流波动大,质量欠佳的锡基巴氏合金线材则容易造成过多的飞溅物,影响增材层的质量和堆焊效率。新型数字化MIG焊工艺将电弧参数反馈和高速伺服送丝系统形成控制闭环,将焊丝的运动与熔滴过渡过程相结合,解决了普通MIG堆焊过程短路、喷射、脉冲过度形成大电流造成熔滴汽化爆断难题,其原理是将焊丝的运动直接与焊接过程结合,熔滴过渡时电流为零,没有颈缩爆断,焊丝回抽运动帮助熔滴脱落与过渡,因此输人的能量更少,电流波动更平稳,堆焊层更平整(新型数字化MIG焊工艺的增材层厚度可比MIG堆焊减小0.5 mm),堆焊效率更高。
此外,数字化电弧加热与多自由度高精密机器人系统(图1)可实现多维、多位置和连续扫描方式沉积,从而实现3D打印,解决了滑动轴承小批量和多品种的复杂工艺问题,通过离线编程方式可真正实现无人化增材制造。
图1 锡基巴氏合金增材制造设备
(未完待续)
(来源:轴承杂志社)
轴研所公众号 轴承杂志社公众号
营销热线
0379-64367521
0379-64880626
13693806700
0379-64886322
0379-64881181