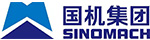
8Cr4Mo4V钢是我国应用较为广泛的一种高温轴承钢,主要用于航空发动机主轴轴承的制造。随着发动机主轴轴承的服役工况愈发恶劣,对材料性能的要求也越来越高,国内外学者开展了大量8Cr4Mo4V钢性能提升的研究工作。作者介绍了8Cr4Mo4V钢化学成分优化的研究进展;重点分析了8Cr4Mo4V钢热处理技术发展,包括传统淬回火、贝氏体等温淬火及尺寸稳定化等热处理工艺;介绍了8Cr4Mo4V钢表面强化技术的研究进展及相关成果,涉及表面合金化、涂层沉积、喷丸强化及复合强化技术;最后,结合8Cr4Mo4V钢服役需求及相关技术研究现状对其后续研究方向进行了展望。
轴承作为航空发动机的关键部件,主要作用是减小发动机各部件之间的摩擦力,传输载荷及保持各部件的准确位置,航空发动机主轴轴承服役环境较为恶劣,其性能直接影响发动机的运行和使用寿命,故航空发动机主轴轴承材料的选择尤为重要。
8Cr4Mo4V(Cr4Mo4V,G80Cr4Mo4V,M50)钢是一种典型的钼系高速钢,其主要合金元素除Mo外还包括大量Cr及V。传统工艺热处理后8Cr4Mo4V钢中存在大量的合金碳化物,保证了其高温硬度及耐磨性。基于8Cr4Mo4V钢优异的力学性能,20世纪80年代中期,美国宇航局开始将其应用于航空轴承。到目前为止,8Cr4Mo4V钢依然是我国应用较为广泛的一种高温(使用温度不大于316 ℃)轴承钢,主要用于发动机主轴轴承的制造。
为进一步提高8Cr4Mo4V钢的性能,近些年国内外学者进行了大量的研究。2020年最新报道显示,国外学者为提高8Cr4Mo4V钢的干摩擦性能,利用放电等离子烧结(Spark Plasma Sintering,SPS)将固体润滑剂(SnS/ZnO)直接加到8Cr4Mo4V钢基体中。
1、8Cr4Mo4V钢化学成分及优化
传统8Cr4Mo4V钢的化学成分见表1,其中质量分数为0.75%~0.85%的C为材料提供了优异的淬透性和硬度。Cr,Mo及V均是强碳化物形成元素,可显著提高材料的耐磨性,其中Cr在8Cr4Mo4V钢中通常以M23C6形式存在,而Mo及V元素主要以M2C和MC形式存在。
表1 8Cr4Mo4V钢化学成分的质量分数 %
文献[7]对8Cr4Mo4V钢失效模式进行了研究,指出其疲劳剥落通常起源于粗大、形状不规则的碳化物。8Cr4Mo4V钢中存在的大块状碳化物有2种:Mo为主的M2C和以无规则块状存在的部分MC。为消除无规则块状碳化物,文献[9]通过热力学计算重新设计了8Cr4Mo4V钢成分(表1中的改进型)并进行了试制,结果表明:通过适当提高Cr含量,同时降低V含量,可使M2C型碳化物尺寸降至5.3 μm以下,球状碳化物M23C6增多;经淬回火处理后改进型8Cr4Mo4V钢的室温硬度不低于64 HRC,400 ℃高温下硬度不低于60 HRC,符合高温轴承的服役要求。由于目前缺乏相关验证,未见到该成分8Cr4Mo4V钢的实际工程应用。
文献[10]研究了Mg对8Cr4Mo4V钢碳化物的影响,结果表明添加少量Mg可改善钢的结晶组织,优化钢锭铸态组织中的网状碳化物。
热处理是决定材料最终性能的关键步骤,为提高8Cr4Mo4V钢性能,研究热处理工艺的改进技术具有重要意义。
2.1 传统热处理技术及其组织性能
国内外8Cr4Mo4V钢传统热处理工艺均为淬火加三次回火,如图1所示,区别在于国外淬火升温过程为一步预热(图1a红线)或三步预热(图1a黑色虚线),而国内基本采用一步预热(图1b);国外淬火冷却过程采用分级淬火方式,主要目的是减小热处理变形,而国内采用吹N2连续冷却。
图1 8Cr4Mo4V钢国内外热处理工艺
Fig.1 Domestic and international heat treatment process of 8Cr4Mo4V steel
淬回火工艺处理后8Cr4Mo4V钢微观组织及物相如图2所示:淬火后8Cr4Mo4V钢的晶粒较为均匀、细小,回火后8Cr4Mo4V钢由回火马氏体、少量残余奥氏体(体积分数不大于3%)及碳化物组成;回火后存在无规则块状和弥散分布小颗粒状碳化物,其中块状碳化物为淬火未溶解碳化物和回火析出碳化物。
图2 淬回火工艺处理后8Cr4Mo4V钢微观组织
Fig.2 Microstructure of 8Cr4Mo4V steel after quenching and tempering process
由文献[8]可知,淬火未溶解碳化物的主要类型为M2C和MC,而回火析出碳化物主要类型为M23C6和M2C。通常,回火析出碳化物尺寸为纳米级,呈片状或球状,可起到二次硬化效果。然而,较早研究中受分析测试手段限制,只能从二维角度对8Cr4Mo4V钢中碳化物进行观察分析,制样以及观察方式均可能导致对其真实形状及尺寸存在误判。随着三维原子探针技术的开发及应用,文献[14]将其用于8Cr4Mo4V钢中碳化物分析,结果如图3所示,图3b和图3c为图3a旋转一定角度的局部放大,回火过程中析出的M2C三维形貌呈细柱状,且连续弥散。
图3 8Cr4Mo4V钢中碳化物三维形貌特征.
Fig.3 Three - dimensional morphology characteristics of car-bides in 8Cr4Mo4V steel
传统淬回火工艺处理后,8Cr4Mo4V钢的微观组织主要包括回火马氏体、极少量残余奥氏体和弥散分布的二次碳化物,室温硬度为60~64 HRC,高温(316 ℃ )硬度可以达到58 HRC,满足大多数主轴轴承服役需求。
2.2 贝氏体等温淬火强韧化工艺
当dn值超过2.0x106 mm.r/min时,韧性不足成为限制8Cr4Mo4V钢使用的主要原因。文献[15-16]相继开展了强韧化技术在8Cr4Mo4V钢热处理工艺中的应用,以达到提高其综合性能和轴承寿命的目的。
金属材料通过等温淬火获得的下贝氏体具有优异的强度和韧性,因此等温淬火是目前较为常用的一种金属增韧工艺。鉴于贝氏体优异的力学性能,文献[24-25]开展了8Cr4Mo4V钢贝氏体等温淬火工艺研究,以进一步提高材料的强韧性。图4a为贝氏体等温淬火工艺处理后8Cr4Mo4V钢的微观组织,图4b为贝氏体等温淬火工艺与常规淬回火工艺的对比,贝氏体等温淬火工艺可以显著提高冲击韧性,提高幅度可达20%~50%。
图4 贝氏体等温淬火后8Cr4Mo4V钢微观组织及性能
Fig.4 Microstructure and properties of 8Cr4Mo4V steel after bainitic austempering
2.3 尺寸稳定化热处理工艺
航空轴承除对力学性能具有较高要求外,还要求其具有优异的尺寸稳定性。8Cr4Mo4V 钢经热处理后尽管残余奥氏体含量(体积分数,下同)已降至3%以下,但在存放和使用过程中依然可能进一步向马氏体转变,从而引起尺寸变化;残余应力的释放也会引起轴承尺寸变化。因此,文献[26]开展了尺寸稳定化热处理工艺对8Cr4Mo4V钢微观组织及尺寸变化的影响,即在轴承正常热处理工序与最终冷加工工序之间增加一个稳定化热处理工序。
8Cr4Mo4V钢稳定化热处理工艺如图5所示,可以看出该工艺包括3个循环,每个循环由冷处理和中温时效2个过程组成。
图5 8Cr4Mo4V钢尺寸稳定化热处理工艺
Fig.5 Dimensional stabilization heat treatment process of 8Cr4Mo4V steel
经不同循环次数的稳定化热处理后,8Cr4Mo4V钢( φ30 mm×20 mm)的残余奥氏体含量及尺寸变化结果如图6所示。由图6a可知:正常热处理后残余奥氏体含量为2.61%,随着尺寸稳定化循环次数的增加,残余奥氏体含量逐渐减少,经3次循环后降低至0.76%。一次稳定处理过程中马氏体析出与残余奥氏体转变同时进行,8Cr4Mo4V钢尺寸整体呈收缩现象(图6b),说明起主要作用的因素为马氏体析出;二次及三次稳定处理时,由于马氏体析出反应基本完成,残余奥氏体向马氏体转变成为引起尺寸变化的主要因素,因此呈现膨胀现象,且随着循环次数的增加,残余奥氏体含量降低,尺寸膨胀量也随之减小。由图6b可知,经三次循环处理后,8Cr4Mo4V钢试样长度平均增加1.5X10-5 mm,变化率为7.5x10-7。
图6 尺寸稳定化热处理循环次数对8Cr4Mo4V钢
残余奧氏体含量及长度的影响
Fig.6 Influence of dimensional stabilization heat treatment cycles on content of residual austenite and length of 8Cr4Mo4V steel
目前,尺寸稳定化热处理缺乏对比试验,后续需开展该工艺对8Cr4Mo4V钢轴承存放或使用过程中尺寸变化的影响研究,以验证该工艺的有效性。
(未完待续)
来源:《轴承》2021年8期
引文格式:周丽娜,杨晓峰,刘明,等.8Cr4Mo4V高温轴承钢热处理及表面改性技术的研究进展[J].轴承,2021(8):1-10.
轴研所公众号 轴承杂志社公众号
营销热线
0379-64367521
0379-64880626
13693806700
0379-64886322
0379-64881181