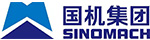
为进一步降低摩擦力矩和减少漏油,NTN开发了汽车变速器用带V形润滑槽密封圈,较常规密封圈摩擦力矩降低60%。
外径为15~60 mm的多种树脂密封圈在汽车变速器(自动变速器、无级变速器等)上使用。为实现汽车的低油耗,这些密封圈要求具有低摩擦力矩和低漏油性能。为响应这一要求,NTN开发了带V形润滑槽的聚醚醚酮(PEEK)树脂低摩擦力矩密封圈(图1),并开始批量生产。
图1 低摩擦力矩密封圈
通过流体分析和试验来优化V形润滑槽的数量和形状,进一步降低低摩擦力矩密封圈的力矩。本文介绍了关于低摩擦力矩密封圈力矩降低的流体分析验证结果。
1、密封圈的功能和应用
密封圈安装在变速器的油压回路内相对运动的轴与壳体之间,起到密封作用。当密封圈滑动时,通过密封油的油压将密封圈推向壳体内表面和轴槽侧壁上,并保持油压回路内部的压力。
密封圈需要具有低摩擦力矩、低漏油性能和高耐磨性。当摩擦力矩降低时,传动效率提高,以实现更高的能源效率。减少漏油使油压泵的效率更高,体积更小,从而使能源效率更高。为了保持低摩擦力矩和低漏油运行,并实现长使用寿命,密封圈需要耐磨,同时防止密封圈滑动配合件的磨损。
带矩形横截面的NTN常规密封圈的应用如图2所示。由于密封圈与轴槽侧壁的接触面积小于密封圈与壳体内表面的接触面积,当轴或壳体旋转时,轴槽侧壁的滑动阻力较小,密封圈在轴槽侧壁上滑动。密封圈与轴槽侧壁是面接触,因此漏油较少。
图2 密封圈的应用
2、低摩擦力矩密封圈
2.1 特征
通过在轴槽侧壁上滑动的密封圈表面设置V形润滑槽,实现低摩擦力矩密封圈的低摩擦力矩和低漏油。密封圈采用在 PEEK树脂中加入特殊添加剂制成的 BEAREEPK5301材料,侧面有注塑成型的V形润滑槽,且对接台阶形状复杂。通过对接台阶的复杂形状减少对接台阶处的漏油。
与NTN常规产品相比,低摩擦力矩密封圈具有以下特征:
1)摩擦力矩降低达60%;
2)1/10的磨损率;
3)相当的低漏油性。
2.2 润滑槽形状的比较
2.2.1摩擦力矩测量结果
具有不同润滑槽形状和无润滑槽的3种密封圈对比见表1。试验设备示意图如图3所示。通过安装在轴槽上的2个密封圈之间的循环油施加油压并旋转壳体,从而实现摩擦力矩的测量。
表1 试验密封圈
注:密封圈外径50 mm,厚度1.6 mm,宽度1.5 mm。
图3 试验设备示意图
油压与摩擦力矩的关系如图4所示。将测得的2个密封圈的摩擦力矩除以2得到1个密封圈的摩擦力矩。带V形润滑槽密封圈的摩擦力矩比无润滑槽密封圈(NTN的常规产品)的低60%~70%,比带方形润滑槽密封圈的低20%。
2.2.2 流体分析结果
摩擦力矩降低的原因被认为是V形润滑槽的应用减小了密封圈与轴槽侧壁的接触面积,改善了滑动表面的润滑。2种形状润滑槽摩擦力矩的差异归因于润滑条件的不同。流体分析证实了这点。
1个润滑槽流体区域模型的分析结果如图5所示。采用V形润滑槽时,由于流体动力效应,润滑槽一端的油膜压力高。油膜压力产生的轴向力与通过油压将密封圈压在轴槽侧壁上的力方向相反,因此可减小油压。还假设由于压力差,油从润滑槽端部流到润滑槽之间的滑动表面,有助于降低摩擦力矩。另一方面,在V形润滑槽中观察到的高油膜压力在方形润滑槽中观察不到。
图4 油压与摩擦力矩的关系
图5 滑动表面的油膜压力分布
3、通过优化V形润滑槽降低摩擦力矩的验证
3.1 流体分析条件
摩擦力矩测量结果和滑动表面的油膜压力分布显示,出现在V形润滑槽端部的力与由于油膜压力(油膜反作用力)导致摩擦力矩降低的力方向相反。油膜反作用力越大,摩擦力矩越低。因此,可认为V形润滑槽数量越多,宽度越宽,油膜反作用力越大。流体分析证实了这点。
分析用密封圈V形润滑槽的长度、宽度、深度、角度以及间距的定义如图6所示。密封圈尺寸为:外径44 mm,厚度2 mm,宽度2.3 mm。基于流体分析对密封圈的1个V形润滑槽的流体区域建模,并对由于流体动力效应产生的油膜压力进行积分得到1个润滑槽的油膜反作用力。将该力与槽数的乘积定义为1个密封圈的油膜反作用力,并进行了不同条件的比较。需注意的是,与V形润滑槽的油膜压力相比,密封圈侧面与轴槽侧壁接触区的油膜压力非常小,可忽略不计。在分析中为便于计算,滑动表面的油膜厚度假定为恒定值5 μm。工作条件设定为:ATF压力0.6 MPa,温度20 ℃,转速1 000r/min。
图6 密封圈的分析(24个槽)
3.2 流体分析结果
3.2.1 V形润滑槽的数量
通过对一侧有12和24个V形润滑槽的密封圈进行流体分析,得到1个密封圈的油膜反作用力。V形润滑槽的间距相同,12和24个槽的长度变化。槽的角度也相同,但12和24个槽的深度不同。
带12和24个V形润滑槽密封圈的油膜反作用力如图7所示。正如所估计的,槽数越多,油膜反作用力越大。因此,槽数越多,摩擦力矩降低越多。
然而,当槽数增加时,槽间的空格数也增加,这增加了密封圈侧面与轴槽侧壁的接触面积,从而导致摩擦力矩升高。因此,应有最优槽数使摩擦力矩最小。为证实这点,制作了不同槽数的密封圈并测量摩擦力矩。密封圈尺寸为:外径51 mm,厚度2.4 mm,宽度2.3 mm。一侧槽数为12~30。槽间距、槽宽、槽角相同,因此槽长和槽深随着槽数不同而不同。测量条件为:ATF压力1 MPa,温度80 ℃,转速2 000 r/min。
图7 槽数与油膜反作用力
槽数与摩擦力矩的关系如图8所示。槽数由12向24增加时,摩擦力矩逐渐降低,但槽数为30时,摩擦力矩增大。测量结果与前述观点一致,证明槽数存在最优值。由于槽数受到设计和制造的限制,从而取决于外径,因此,NTN低摩擦力矩密封圈按照外径尺寸排列了最优数量的V形润滑槽。
图8 槽数与摩擦力矩的关系
3.2.2 V形润滑槽的宽度
通过对带宽度为0.2~0.7 mm 的V形润滑槽的密封圈进行流体分析,得到油膜反作用力。密封圈一侧的槽数为24,除槽宽外,其他尺寸都相同。
槽宽与油膜反作用力的关系如图9所示。验证结果与估算结果一致,油膜反作用力随着槽宽增加而增大,但过大的槽宽会导致漏油量增大。因此,必须针对每种情况确定槽宽,要考虑轴和壳体的尺寸、偏心率、密封圈和壳体的磨损量等。
图9 槽宽与油膜反作用力的关系
3.2.3 V形润滑槽的角度
基于4.2.1节中描述的一侧有24个槽的密封圈,通过增大或减小V形润滑槽的角度,采用流体分析得到油膜反作用力。槽间距、槽宽和槽长相同,只有槽角变化而导致的槽深不同。
槽角与油膜反作用力的关系如图10所示。在试验的角度范围内,无论槽角如何,油膜反作用力几乎相同。同样地,槽深也没有影响。这些结果表明在V形润滑槽的设计中必须关注槽数,如果槽深和槽角在适当的范围内,则不需要考虑。
图10 槽角与油膜反作用力的关系
3.3 带最优V形润滑槽密封圈的摩擦力矩
测量结果
基于上面的流体分析优化了V形润滑槽的数量和形状。优化后的带24个V形润滑槽密封圈与3.2节中讨论的带12个V形润滑槽密封圈的摩擦力矩对比结果如图11所示。优化后的带24个V形润滑槽密封圈的摩擦力矩比带12个槽的降低了10%~15%。测量中选用外径45 mm、厚度2 mm、宽度2.4 mm的密封圈进行比较。
图11 油压与摩擦力矩的关系
4、结束语
介绍了关于低摩擦力矩密封圈摩擦力矩降低的流体分析验证结果。基于流体分析和试验,优化了V形润滑槽的数量和形状,进一步降低了摩擦力矩。低摩擦力矩密封圈的采用进展良好,因为其能响应车辆低油耗的要求。未来将致力于进一步降低摩擦力矩。
在许多领域对能源效率的要求不断提高,将采用流体分析等分析方法加快开发速度,提高树脂滑动部件的性能。
(参考文献略)
Verification of Torque Reduction for Low Torque Seal Ring by Fluid Analysis
来源:《NTN TECHNICAL REVIEW》
作者:Takuya ISHII等
翻译:侯万果
校对:曾献智
整理、排版:轴承杂志社
轴研所公众号 轴承杂志社公众号
营销热线
0379-64367521
0379-64880626
13693806700
0379-64886322
0379-64881181